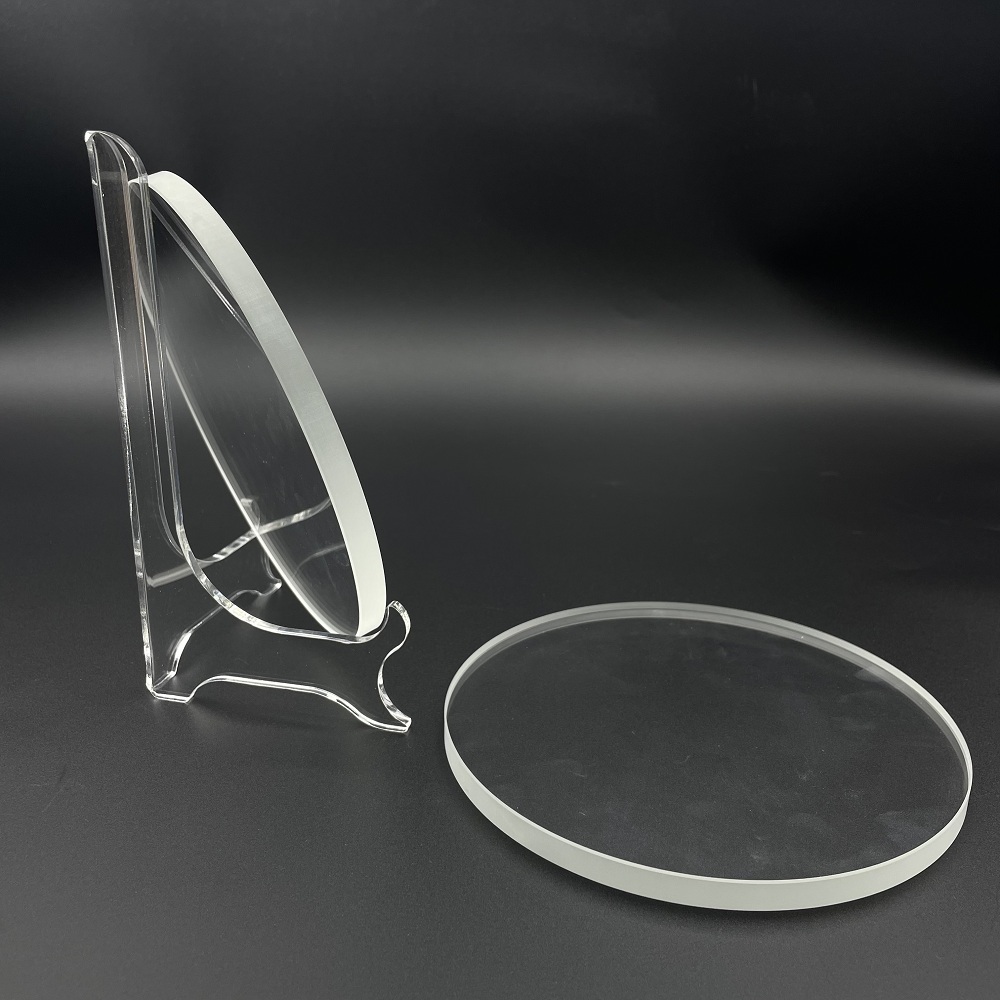
Fused Silica JGS3 Glass Wafer
Glass Wafer

-
+86-17701852595 WhatsApp
-
sales@plutosemitech.com Email
Fused Silica JGS3 Glass Wafer is a high-performance material primarily made of SiO2 (silicon dioxide), offering exceptional properties for demanding applications. With a density of 2.2 g/cm³ and a melting point of 1730°C, it exhibits excellent thermal stability and resistance to high temperatures. Its Moh's hardness of 7 ensures durability, while its high resistance to rapid temperature changes (800-1100°C) makes it ideal for environments with thermal cycling. Available in sizes ranging from 2 to 12 inches, this transparent, high-purity wafer is produced using the gas refining method, ensuring high precision and consistency. As a leading China fused silica wafer supplier, we specialize in offering top-quality Fused Silica JGS3 Glass Wafers designed for high-tech industries.
Product Name: Fused Silica JGS3 Glass Wafer
Size: 2/4/6/8/12inch or customized
Package: Hundred-class clean room
Customized Support: YES
RoHS: YES
Delivery Methods: Logistics Express
Marketable Area: oversea
Growth Method: Gas refining method/Synthesis
Base: SiO2
Density: 2.2g/cm3
Melting Point: 1730℃
Moh's Hardness: 7
Maximum safe operating temperature (continuous): 1000-1100℃
Maximum safe operating temperature (short time): 1300-1400℃
Resistance to rapid change in temperature: 800-1100℃
Thermal Expansion Coefficient: 5.4×10-7
Dislectric Constant(0~106 Hz): 3.7(Normal Temperatures)
Conductivity(S/m): 10-17~10-16(20℃)
Color: Transparent
Fused Silica JGS3 Glass Wafer Specifications
Grade | Product Name | Applied spectral band range(um) |
JGS3 | Fused Silica Glass Wafer | 0.26-3.5 |
JGS3 Fused Silica Glass Wafer Transmittance
Classification | Transmittance of 10mm thick blanks(%) | ||||
2.0um | 2.5um | 2.7um | 2.8um | 0.2-2.8um | |
1 | >90 | >90 | >90 | >85 | no absorption peak |
2 | >85 | >85 | >85 | >80 | no absorption peak |
3 | >80 | >80 | >75 | >75 | Absorption peaks are allowed |
Technical Specifications | |||||||
Diameter | 2inch | 3inch | 4inch | 5inch | 6inch | 8inch | 12inch |
Thickness (um) | Depends on Request | ||||||
Material | Borofloat33 | ||||||
Grade/Brand | SCHOTT | ||||||
Surface Finished | DSP、SSP、DSL | ||||||
TTV (um) | <5 | <5 | <5 | <5 | <5 | <10 | <15 |
Bow/Warp (um) | <20 | <20 | <30 | <30 | <30 | <40 | <60 |
Ra (nm) | <1 | ||||||
S/D (um) | 40/20 |
Special Indexes:
Ultra-flat glass wafer: TTV<1um
Ultra-thin glass wafer: Thickness: 0.1-0.3um
Ultra-smooth glass wafer: Ra≤0.2nm
Fused Silica JGS3 Glass Wafer Features
1. High Purity SiO2 Base: Made from high-quality silicon dioxide (SiO2), ensuring excellent material properties and reliability in demanding applications.
2. Wide Size Range: Available in standard sizes of 2, 4, 6, 8, and 12 inches, with customizable sizes to meet specific customer requirements.
3. Excellent Thermal Stability: With a melting point of 1730°C, the wafer offers superior resistance to high temperatures, making it suitable for extreme thermal environments.
4. High Moh’s Hardness (7): The material has a Moh’s hardness of 7, ensuring durability and resistance to wear and mechanical stress.
5. Low Thermal Expansion: With a thermal expansion coefficient of 5.4×10, the wafer exhibits minimal expansion or contraction in response to temperature changes, ensuring dimensional stability.
Fused Silica JGS3 Glass Wafer FAQ
What is the main material used in the Fused Silica JGS3 Glass Wafer?
The wafer is primarily made of high-purity SiO2 (silicon dioxide), ensuring excellent quality and stability for demanding applications.
What sizes are available for the Fused Silica JGS3 Glass Wafer?
The wafer is available in standard sizes of 2, 4, 6, 8, and 12 inches, with custom sizes available upon request.
What is the maximum temperature the Fused Silica JGS3 Glass Wafer can withstand?
The wafer can operate continuously at temperatures between 1000-1100°C, and can withstand short-term exposure to temperatures up to 1300-1400°C.
Is the Fused Silica JGS3 Glass Wafer resistant to rapid temperature changes?
Yes, it is highly resistant to rapid temperature changes, withstanding temperature fluctuations from 800-1100°C.
Packaging and Transportation
The packaging should be able to withstand the impact, vibration, stacking and extrusion that may be encountered during transportation, while also it has to easy to load, unload and handle.
We use professional wafer box packaging. The wafer box is protected by a double layer bag, the inside is a PE bag that can be dust-proof, and the outside is a aluminum foil bag that can be isolated from the air. The two-layer bags are vacuum-packed.
We will choose carton models according to different sizes of products. And between the product and the carton filled with shock-proof EPE foam, play a comprehensive protection.
Finally choose air transport to reach the customer's hands. This allows customers in any country and region to receive the product in the fastest time.
We comply with the Material Safety Data Sheet (MSDS) rules to ensure that the products transported are free of harmful substances and will not cause environmental pollution and explosion and other possible hazards.
Enterprise Strength
Factory Area: 3000 sq
Process:
1. Shaping→2. Edge Profile→3. Lapping→4. Polishing→5. Cleaning→6. Packing→7. Transportation
Capacity:
Glass Wafer --- 30K pcs
Silicon Wafer --- 20K pcs
(Equal to 6in)
Quality Assurance
Quality inspection method: Product inspection in accordance with SEMI standard or according to customer's requirements, together with product COA.
Warranty period: In accordance with the contract requirements.
Quality system management:
●Organize production according to ISO9001 and other quality system standards.
Quality management system and measures:
●Establish a strict quality assurance system, the heads of all departments and quality engineers to ensure the coordinated operation of the quality system.
●Strengthen the quality inspection system, strengthen the process quality control
●Strict material quality control, ensure that the input materials meet the design requirements and technical specifications.
●Implement a timely filing system for technical data to ensure that all processing technical data is complete/accurate.
Quality control in the production stage:
●Production preparation stage: carefully organize relevant personnel to learn product drawings and technical rules, and improve the technical level of employees.
●Quality control of the production process: the implementation of a strict handover system, the previous step of the process to the next step of the transfer, should be detailed processing. At the same time, strengthen the quality inspection system to ensure the quality of each step of the process.
●Quality acceptance: All processes must be quality acceptance before proceeding to the next process.
Pre-sales and After-sales
Pre-sales Service
Professional technical support and commercial team to help you determine product specifications according to product use, and issue specifications.
On-purchase Service
Produce products according to the confirmed specifications and our process.
After Sale Service
We will respond to any product problems encountered by customers or process problems encountered by customers within 24 hours. We can choose from various forms of service, such as email, video conference and so on.
Plutosemi Co., Ltd. was established in 2019, headquartered in Nanhai, Foshan, focusing on the research and development, production, and sales of high-performance semiconductor materials.
Advanced production capacity: We have three major production bases in China, with a monthly production capacity of 100000 equivalent 6-inch silicon wafers and 30000 equivalent 8-inch glass wafers, ensuring stable and efficient product supply for our customers.
High quality products: We provide efficient and stable product supply innovative solutions in the fields of glass wafers, silicon polishing wafers, epitaxial wafers (EPI), silicon on insulator wafers (SOI), and more. Our silicon wafers have the characteristics of ultra-thin, ultraflat, and high-precision, which can meet the needs of various high-end applications. Our glass and quartz substrates are also renowned for their high smoothness and precise aperture design.