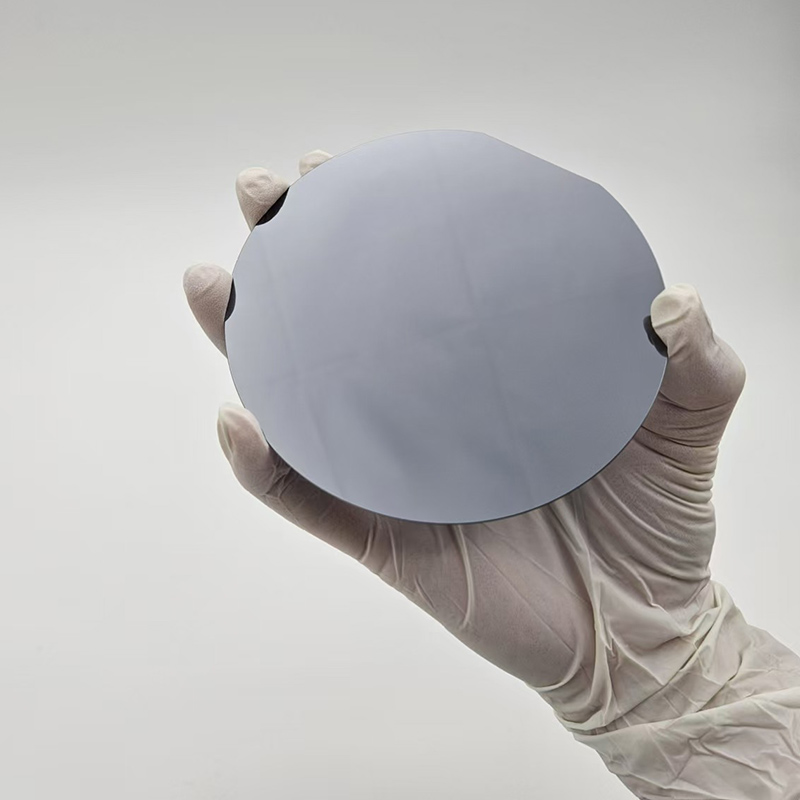
Low Resistance Silicon Wafer
Silicon Wafer

-
+86-17701852595 WhatsApp
-
sales@plutosemitech.com Email
Low Resistance Silicon Wafer is a special type of silicon wafer characterized by its extremely low electrical resistivity. The low resistance characteristics of this silicon wafer are mainly achieved through precise doping processes. Doping refers to introducing a small amount of impurity elements (such as boron or phosphorus) into silicon crystals to change their conductivity. By controlling the concentration and type of doping, the resistivity of silicon wafers can be significantly reduced, making them more suitable for high-performance semiconductor devices. The manufacturing process of Low Resistance Silicon Wafer requires extremely high precision and purity to ensure the stability and consistency of its electrical performance.
Low Resistance Silicon Wafer Specifications
Diameter | 2" | 3" | 4" | 5" | 6" | 8" | 12" |
Grade | Prime Test Dummy | ||||||
Growth Method | CZ | ||||||
Orientation | < 1-0-0 >, < 1-1-1 >, < 1-1- 0> | ||||||
Type/Dopant | P Type/Boron, N Type/Phos, N Type/As, N Type/Sb | ||||||
Thickness(um) | 279 | 380 | 525 | 625 | 675 | 725 | 775 |
Thickness Tolerance | Standard ±25μm, Maximum Capabilities ±5μm | ±20μm | ±20μm | ||||
Resistivity | >100 ohm-cm | ||||||
Surface Finished | P/E, P/P, E/E, G/G | ||||||
TTV(um) | Standard < 10um, Maximum Capabilities < 5um | ||||||
Bow/Warp(um) | Standard < 40um, Maximum Capabilities < 20um | < 40μm | < 40μm | ||||
Particle | < 10@0.5um; < 10@0.3um; < 10@0.2um |
Low Resistance Silicon Wafer Features
1. Low resistivity:
The resistivity of Low Resistance Silicon Wafer is significantly lower than that of ordinary silicon wafers, typically ranging from 0.001 Ω - cm to 1 Ω - cm. Low resistivity means that silicon wafers have less energy loss when transmitting electrical signals, thereby improving the overall efficiency and response speed of the device.
2. High carrier concentration:
The carrier concentration of Low Resistance Silicon Wafer is significantly higher than that of ordinary silicon wafers, which is also one of the key reasons for its low resistivity. The carrier concentration makes silicon wafers more efficient in transmitting current, reduces energy loss, and is suitable for high-power and high-frequency applications. High carrier concentration also brings higher temperature sensitivity, which needs to be controlled in the design and manufacturing process to ensure the reliability of the device in complex working environments.
3. Higher doping concentration:
The low resistivity of Low Resistance Silicon Wafer mainly relies on high concentration doping process. Common dopants include phosphorus (donor doping) and boron (acceptor doping), which can effectively alter the conductivity of silicon wafers. This process requires precise control of doping concentration to ensure that the electrical properties of silicon wafers meet specific application requirements.
4. Temperature stability:
The stability of Low Resistance Silicon Wafer is poor in high-temperature environments, which is closely related to its high carrier concentration. Due to the high carrier concentration, temperature changes can significantly affect the resistivity of silicon wafers, leading to instability in device performance. Under high temperature conditions, the mobility and recombination rate of charge carriers will change, thereby affecting the conductivity of silicon wafers.
Low Resistance Silicon Wafer Manufacturing Process
Doping process: Low resistance silicon wafers are manufactured with a high concentration of dopant and are usually heavily doped, such as high dose ion implantation or high temperature diffusion.
Annealing: The annealing process for LRWs is equally important, but the temperature and time control needs to be more precise to avoid high resistivity.
Surface treatment: The surface treatment of low-resistance wafers also needs to be tightly controlled to ensure that the surface quality meets the requirements, especially in the manufacture of power devices.
Low Resistance Silicon Wafer Application
1. Power Devices:
Low Resistance Silicon Wafer is widely used in power devices, especially high-performance semiconductor devices such as MOSFETs (Metal Oxide Field Effect Transistors) and IGBTs (Insulated Gate Bipolar Transistors). These devices require low resistance to reduce power loss, thereby improving efficiency and heat dissipation performance. MOSFETs require low resistance silicon wafers to reduce driving resistance and minimize energy loss during turn-on and turn off. IGBTs utilize it to optimize switching speed and thermal conductivity, thereby improving their performance in high voltage and high current environments.
2. Digital Circuits:
The applications in digital circuits mainly focus on scenarios requiring high-speed switching and high current driving. For example, in high-performance microprocessors, high-speed communication chips, and large capacity storage devices, it can significantly reduce energy loss in signal transmission, improve signal integrity and transmission speed. Especially in high-speed logic gates and high-speed data transmission interfaces, low resistance silicon wafer can significantly improve the response speed and data transmission rate of circuits, meeting the demands of modern electronic devices for high-performance computing and communication.
3. Solar Cells:
It is also widely used in traditional solar cells, especially in situations where high current output is required. By reducing the resistance of silicon wafers, the conversion efficiency and output power of batteries can be improved. The low resistance characteristic helps to reduce energy loss in photovoltaic systems and improve the overall efficiency of the system. For example, in large-area photovoltaic panels and high-power photovoltaic systems, the application of low resistance silicon wafers can enable photovoltaic cells to generate higher current output under the same lighting conditions, thereby improving the system's power generation capacity and economy.
4. Sensor applications:
The application of low resistance silicon wafers in high-precision sensors is becoming increasingly common. For example, temperature sensors, pressure sensors, and acceleration sensors require low resistance for signal transmission to reduce noise and errors during the measurement process. It can provide more stable signal transmission characteristics, ensuring high precision and reliability of the sensor. This characteristic makes it an ideal choice for applications such as temperature and pressure sensors.
5. Laser applications:
The application of low resistance silicon wafer in high-performance lasers is of great significance. Laser has extremely high requirements for the resistivity and conductivity of materials, and low resistance silicon wafer can provide more stable current transmission, thereby improving the efficiency and stability of laser operation. Especially for high-power lasers, they can maintain good conductivity under high current and high-speed operating conditions, ensuring excellent performance in high-performance and high reliability applications.
6. Storage devices:
It is also widely used in storage devices, especially in high-performance memory and high-capacity storage media. For example, in storage devices such as solid-state drives (SSDs) and memory cards, low resistance silicon wafers can optimize energy loss during data transmission and storage processes, improving the read and write speed and durability of storage systems. The low resistance characteristic helps to reduce the energy consumption of storage devices during operation, extend their service life, and improve the overall performance of the system.
Packaging and Transportation
The packaging should be able to withstand the impact, vibration, stacking and extrusion that may be encountered during transportation, while also it has to easy to load, unload and handle.
We use professional wafer box packaging. The wafer box is protected by a double layer bag, the inside is a PE bag that can be dust-proof, and the outside is a aluminum foil bag that can be isolated from the air. The two-layer bags are vacuum-packed.
We will choose carton models according to different sizes of products. And between the product and the carton filled with shock-proof EPE foam, play a comprehensive protection.
Finally choose air transport to reach the customer's hands. This allows customers in any country and region to receive the product in the fastest time.
We comply with the Material Safety Data Sheet (MSDS) rules to ensure that the products transported are free of harmful substances and will not cause environmental pollution and explosion and other possible hazards.
Enterprise Strength
Factory Area: 3000 sq
Process:
1. Shaping→2. Edge Profile→3. Lapping→4. Polishing→5. Cleaning→6. Packing→7. Transportation
Capacity:
Glass Wafer --- 30K pcs
Silicon Wafer --- 20K pcs
(Equal to 6in)
Quality Assurance
Quality inspection method: Product inspection in accordance with SEMI standard or according to customer's requirements, together with product COA.
Warranty period: In accordance with the contract requirements.
Quality system management:
●Organize production according to ISO9001 and other quality system standards.
Quality management system and measures:
●Establish a strict quality assurance system, the heads of all departments and quality engineers to ensure the coordinated operation of the quality system.
●Strengthen the quality inspection system, strengthen the process quality control
●Strict material quality control, ensure that the input materials meet the design requirements and technical specifications.
●Implement a timely filing system for technical data to ensure that all processing technical data is complete/accurate.
Quality control in the production stage:
●Production preparation stage: carefully organize relevant personnel to learn product drawings and technical rules, and improve the technical level of employees.
●Quality control of the production process: the implementation of a strict handover system, the previous step of the process to the next step of the transfer, should be detailed processing. At the same time, strengthen the quality inspection system to ensure the quality of each step of the process.
●Quality acceptance: All processes must be quality acceptance before proceeding to the next process.
Pre-sales and After-sales
Pre-sales Service
Professional technical support and commercial team to help you determine product specifications according to product use, and issue specifications.
On-purchase Service
Produce products according to the confirmed specifications and our process.
After Sale Service
We will respond to any product problems encountered by customers or process problems encountered by customers within 24 hours. We can choose from various forms of service, such as email, video conference and so on.
Plutosemi Co., Ltd. was established in 2019, headquartered in Nanhai, Foshan, focusing on the research and development, production, and sales of high-performance semiconductor materials.
Advanced production capacity: We have three major production bases in China, with a monthly production capacity of 100000 equivalent 6-inch silicon wafers and 30000 equivalent 8-inch glass wafers, ensuring stable and efficient product supply for our customers.
High quality products: We provide efficient and stable product supply innovative solutions in the fields of glass wafers, silicon polishing wafers, epitaxial wafers (EPI), silicon on insulator wafers (SOI), and more. Our silicon wafers have the characteristics of ultra-thin, ultraflat, and high-precision, which can meet the needs of various high-end applications. Our glass and quartz substrates are also renowned for their high smoothness and precise aperture design.